About NDT & How Eddy Current Works
Non-Destructive Testing (NDT), a.k.a Non Destructive Inspection (NDI) or NonDestructive Evaluation (NDE):
The examination of object materials and/or components without destroying or impacting the integrity of the inspected sample. Eddy Current Testing (ECT or ET) is one of several different NDT inspection methods. Visit ASNT.org to learn about other testing methods.
Electromagnetic testing (ET) is a Non-Destructive Testing (NDT) method that uses electromagnetic induction for detection of surface-breaking and sub-surface flaws. Eddy current testing (ECT), also known as eddy current flaw detection, is a type of electromagnetic nondestructive testing.
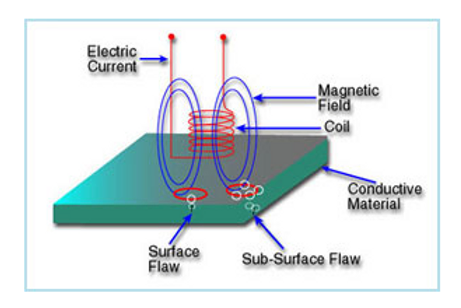
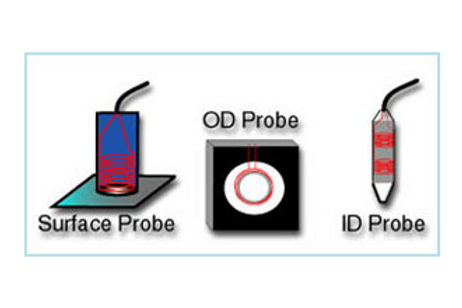
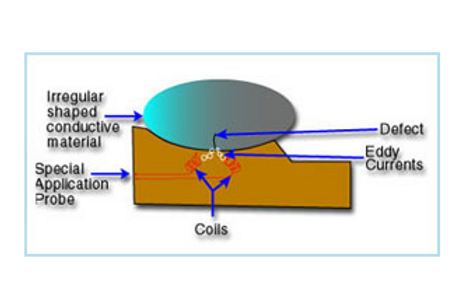
Understanding Coils
A coil of copper wire is the common method of inducing eddy currents. Alternating current running through a coil creates magnetic fields in and around the coil. The magnetic fields form loops around the wire and join to form larger loops. If the current increases in one loop, the magnetic field will expand across some or all of the loops of wire that are in close proximity. This induces a voltage in the neighboring loops and causes electron flow, or eddy currents, in electrically conductive material. Any defect in the material including changes in wall thickness, cracks, pitting and other discontinuities, change the flow of eddy currents and are measurable on eddy current instruments. The enhanced eddy current systems offered by UniWest provide superb sensitivity with the clearest display for a wide range of applications.
Inductance
Alternating current running through a coil creates a magnetic field in and around the coil that is building and collapsing as the current changes. As current increases, the coil becomes more magnetic and induces circulating (eddy) currents in conductive material that is near the coil. The amplitude and phase of the eddy currents will change the loading of the coil and its impedance. If a surface or sub-surface discontinuity exists in a conductive material, the eddy currents will be interrupted and the flow can be measured by UniWest’s instruments. UniWest offers single channel / single frequency, single channel / dual frequency, and multi-channel instruments. Multi-channel detects and measures several flaws simultaneously. Frequencies range from 100 Hz to 10 MHz so that several types of materials can be analyzed for defects. Higher frequencies typically find cracks closer to the surface and lower frequencies penetrate further into the sub-surface of materials.
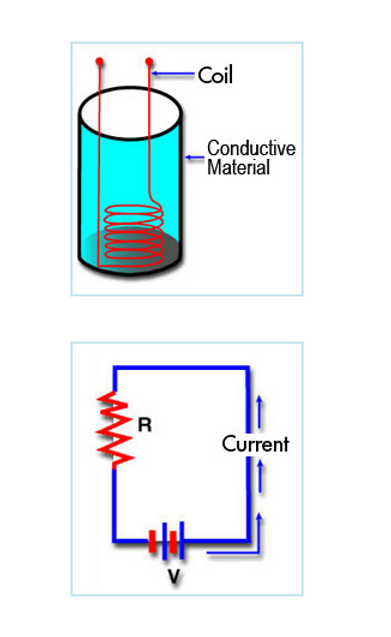
Magnetic Fields
The illustration on the below shows how electric currents form magnetic fields in coils. The coils in turn, form eddy currents in conductive material and also form their own magnetic fields. If a sub-surface discontinuity exists, the eddy current method will find it unless a crack is lying parallel to the current’s path. When a crack is parallel to the current it may not cause a disruption of continuity and therefore won’t show the flaw.
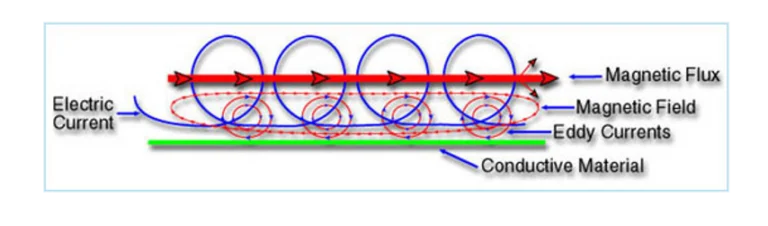
Flaw Detection
Changing the voltage across the coil will affect the material being scanned and allow the eddy current instrument to measure surface and sub-surface discontinuities. Several factors will influence the way flaws can be detected including the following: The conductivity of the material has a dramatic effect in the way eddy currents travel through the surface and sub-surface of materials. The more conductive the material is, the greater the flow of eddy currents. Permeability of the conductive material also has a dramatic effect because of its ability to be magnetized. Geometry plays an important role in detection as well. A flat surface is much easier to scan than an irregular surface. UniWest produces several special application probes that are contoured to the part being scanned for consistent coil placement throughout the specified depth of penetration. Depth of penetration makes a significant difference in the success of the inspection. A surface crack is much easier to detect than a sub-surface flaw. Selection of the proper frequency is critical to finding flaws. How the coil is configured, how many wraps, what size wire and where the coil is placed in the probe all make significant changes in the way defects are seen. Since the surface area is being magnetized, one of the most important factors in determining flaws is contact with the surface and lift off. When the coil is lifted from the surface, magnetic energy stops and eddy currents cease to exist. Even a small amount of lift off can have dramatic effects on the decrease of currents.
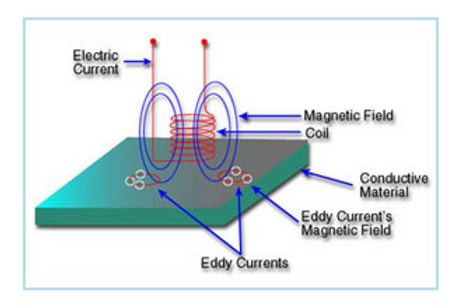
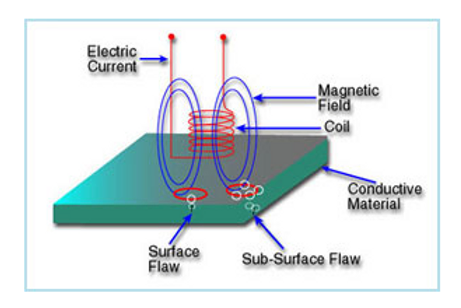
Contour Flaw Detection
There are hundreds of standard and special application probes that are produced for specific surface types and contours. Edges, grooves, contours, circumferentiation and metal thickness all contribute to the success or failure of the testing. A coil that is positioned close to the surface of the conductive material will have the best chance of discovering discontinuities. For difficult contours a coil is inserted into a special shoe and attached to a fixture that will allow the coil to traverse close to the suspect section. Many applications require special shaped probe bodies and coils to adapt to the irregular shape of the part. The coil may also be shaped to fit the design of the part. UniWest special application probes are well known in the eddy current industry for innovative crack detection on hard to inspect contours.
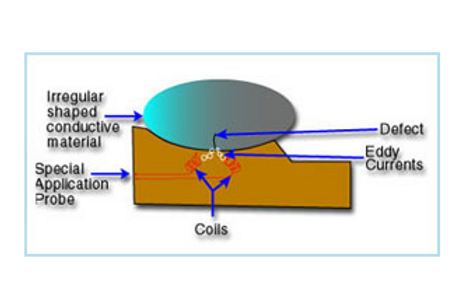
Eddy Current Probes
Three major types of eddy current probes are surface, outside diameter and inside diameter. These three configurations, as well as some cross over designs, are used for most flaw detection applications. Absolute probes have single coil design and give an ‘absolute’ reading at the flaw. Differential probes use two coils to check for flaws in different areas or to differentiate between two variables. Reflection probes have a primary coil being supplied by the oscillator and at least one coil from the measurement circuit. Reflection probes can be either absolute or differential.
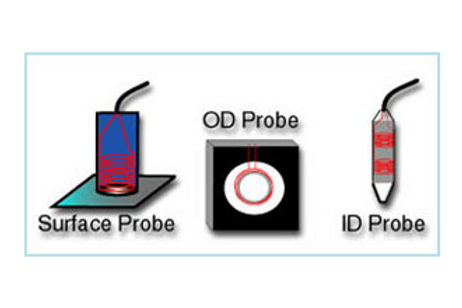
Ohm’s Law and Other Formulas
Ohm’s Law is one of the most basic formulas to determine electrical flow. The voltage, divided by resistance in Ohms, determines electrical current, in Amperes.
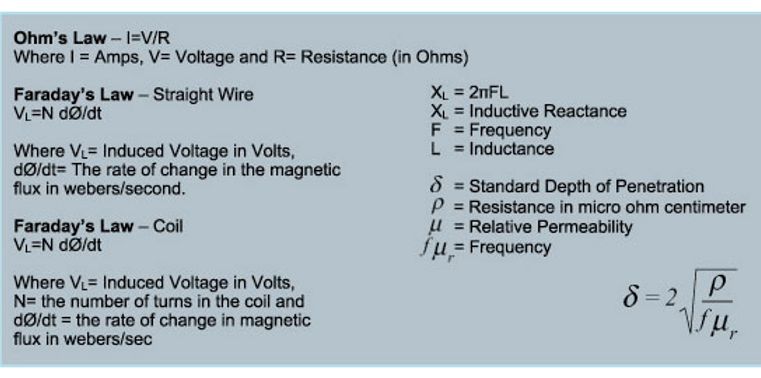
Reach Out To Us
Ready for more information or an on-site demonstration?
Click the button below to get started!